Case Study: Successful Welding Repairs in Michigan's Harsh Winters
Introduction to Welding Challenges in Michigan
Michigan's winters are notorious for their harshness, with temperatures often plummeting well below freezing. This extreme weather can pose significant challenges for various industries, particularly those reliant on welding repairs. The combination of cold temperatures and moisture can lead to metal brittleness and increased difficulty in achieving strong, durable welds.

Despite these challenges, many companies in Michigan have developed innovative strategies to ensure successful welding repairs during the winter months. This case study explores these strategies and highlights the key factors that contribute to effective welding in such an unforgiving environment.
Understanding the Impact of Cold Weather on Welding
Cold weather can significantly affect welding processes and outcomes. The primary issues include:
- Metal Brittleness: Low temperatures can cause metals to become brittle, increasing the risk of cracking during and after welding.
- Moisture Accumulation: Snow and ice can introduce moisture into the welding area, leading to porosity in the welds.
- Equipment Malfunctions: Cold weather can cause welding equipment to perform less efficiently or even malfunction.
Understanding these challenges is crucial for developing effective strategies to mitigate their impact and ensure the integrity of welding repairs.
Innovative Solutions for Winter Welding
Several companies in Michigan have adopted innovative solutions to address the challenges of welding in cold weather. Some of these solutions include:
- Preheating Techniques: Preheating the metal before welding helps reduce brittleness and improves weld quality.
- Controlled Environments: Creating temporary shelters or using heated tents to maintain a stable temperature around the welding area.
- Specialized Equipment: Utilizing equipment designed to function optimally in low temperatures.
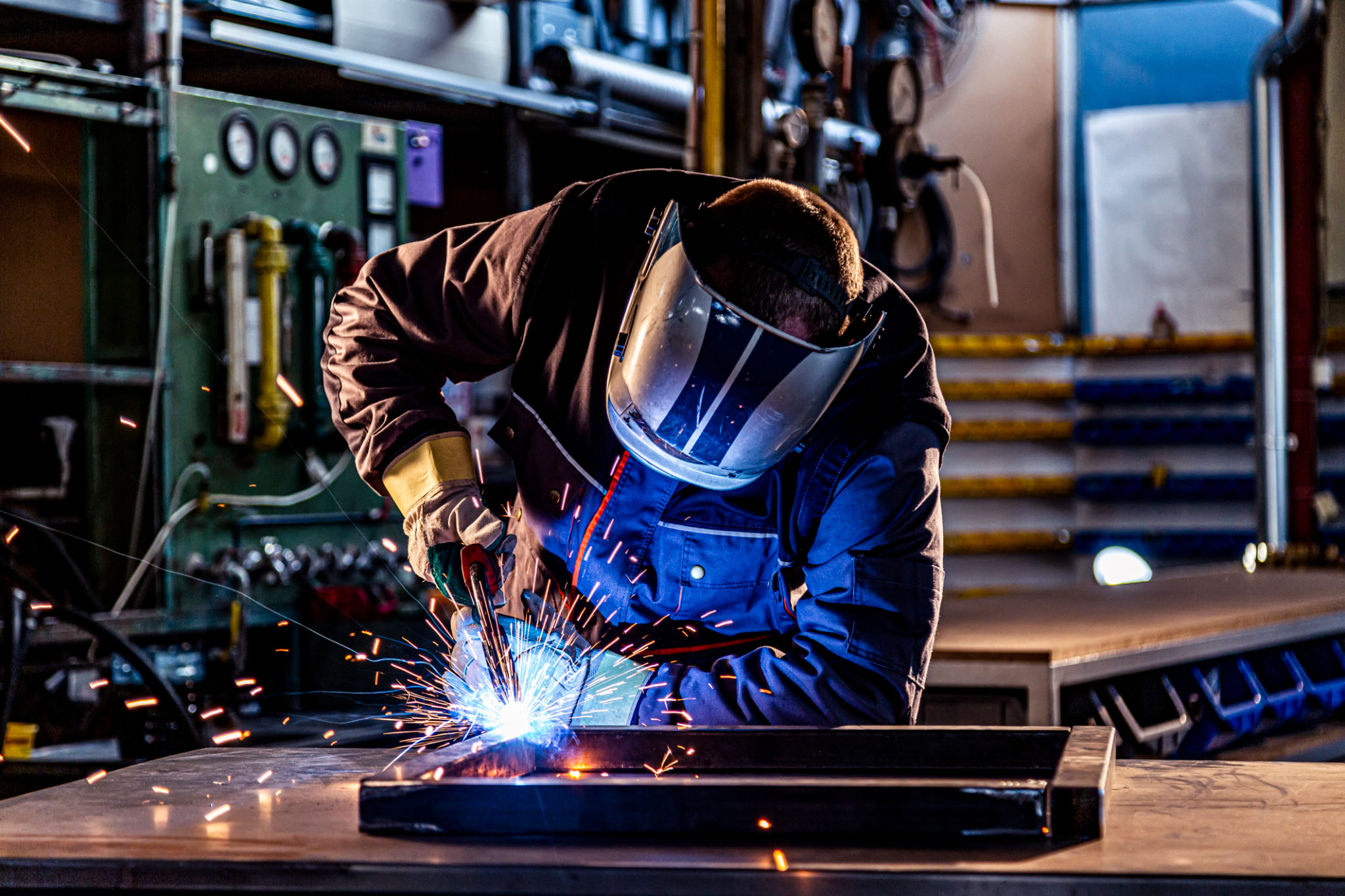
By implementing these strategies, companies can significantly enhance the quality and durability of their welding repairs, even in the harshest winter conditions.
Case Study: A Success Story
One notable success story comes from a Michigan-based construction company that specializes in infrastructure repairs. Faced with the challenge of maintaining bridges during winter, the company developed a comprehensive approach to welding repairs that included all the aforementioned strategies.
By investing in high-quality preheating equipment and constructing insulated shelters around their work sites, the company was able to complete several critical repair projects on schedule and without compromising on quality. Their innovative approach has since become a model for other companies facing similar challenges.
Lessons Learned and Best Practices
This case study offers several valuable lessons and best practices for companies looking to improve their winter welding operations:
- Invest in proper training for welders to handle cold-weather conditions effectively.
- Regularly maintain and inspect equipment to ensure optimal performance in low temperatures.
- Collaborate with industry experts to stay updated on the latest technologies and techniques.
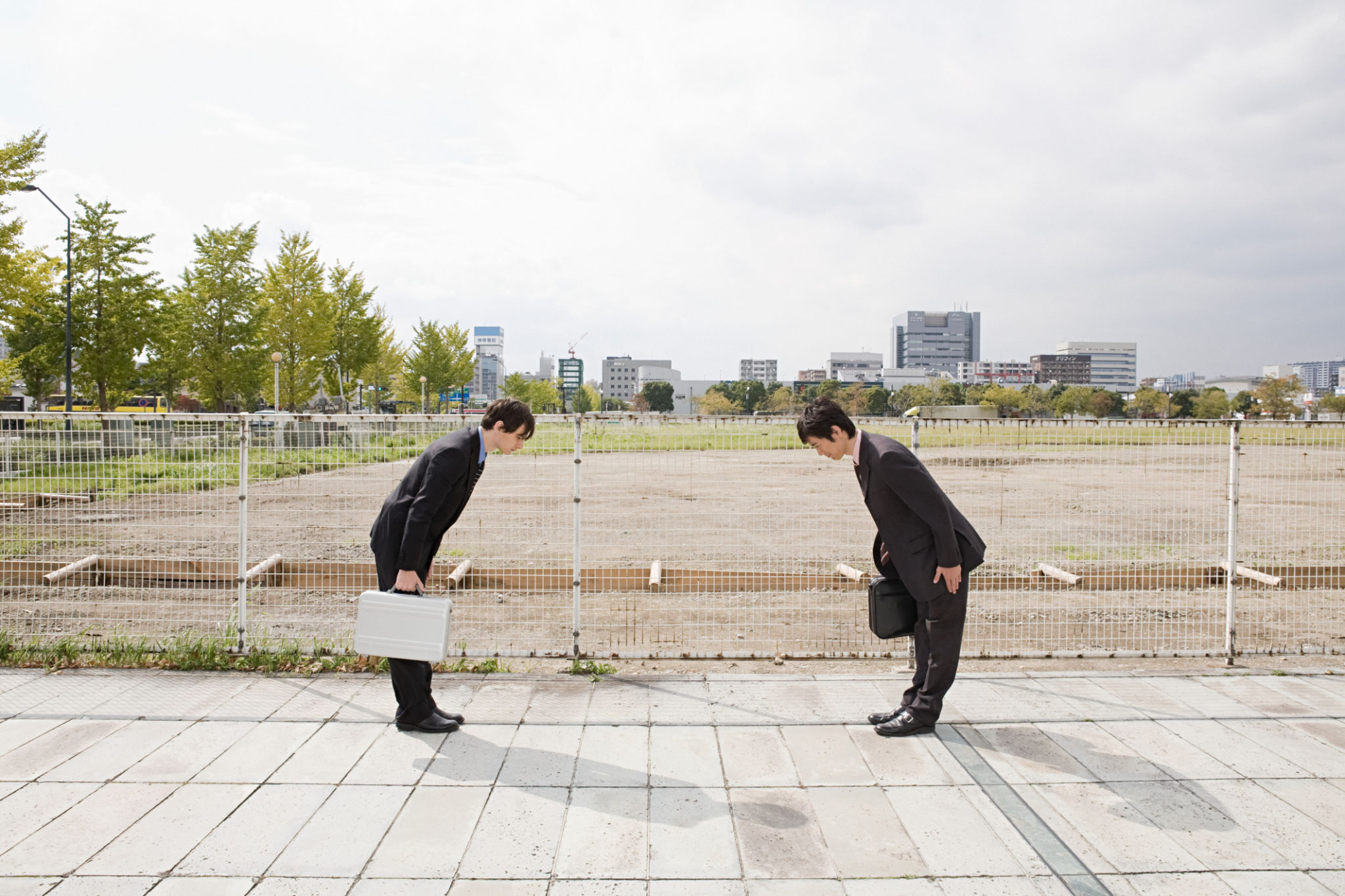
By following these best practices, companies can not only overcome the challenges of winter welding but also improve overall efficiency and safety in their operations.
Conclusion: Embracing Innovation for Success
Welding repairs during Michigan's harsh winters present unique challenges that require innovative solutions. By understanding the impact of cold weather on welding processes and adopting effective strategies, companies can achieve successful outcomes and maintain the integrity of their projects.
The case study highlights the importance of innovation and adaptability in overcoming environmental challenges. As companies continue to embrace new technologies and techniques, they can ensure the long-term success and sustainability of their operations in any weather condition.